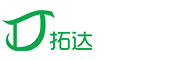
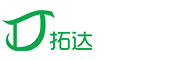
减速机箱体振动时效现场
φ660开炼机减速箱壳体
振动时效处理工艺及效果检测
大连冰山橡塑集团是我国生产橡塑机械的企业之一,每年都有大量的铸件和焊接构件需要经时效处理来应力。过去均采用热时效处理,近十年来,由于产量的增加,热时效处理跟不上生产的需要,又增加了振动时效处理,保证了生产。由于企业的发展及产品产量的大幅增加,也是由于希望通过工艺的改进而节省大量能源,故提出在大型焊接构件和大型铸件上均采用振动时效代替热时效。为观测振动时效的效果和优化原有振动时效工艺规程,厂方提出在选购振动时效设备的同时,对φ660开炼机减速箱壳体(上、中、下三件)做振动时效工艺的优化,并通过应力检测,确定时效的效果和对振动时效设备可靠性的考验。
经过双方的共同努力,做了多次的减速箱壳体类及大型焊接底座的振动时效处理试验,证明了设备的适用性及振动时效在这些构件上应用的可行性。***后又通过对φ660开炼机减速机箱体(上、中、下三件)的正式处理及振动处理前后的残余应力检测,说明了振动时效在内应力上达到了国家(JB/T5926.91)标准,工艺可行,设备性能可靠适用。
一、φ660开炼机减速箱壳体振动时效处理
1、振动时效处理对金属构件的作用
振动时效是对具有残余应力的金属构件进行振动处理,使构件在共振频率下振动。由于在共振状态下构件按一定的振型产生弹性变形,当这个动应力与构件上各点的残余应力相叠加后,大于材料的屈服极限时,则在该点出现局部的塑性变形,因而应力得到释放。振动时效从原理上来说,就是降低构件内的残余应力。应力降低的水平与构件内的动应力大小有关,动应力大则效果高,动应力小则应力的效果低。
振动时效既然可以降低应力,则必然可以残余应力对构件的影响。其作用有如下几方面:
(1)降低和均化应力,应力集中,防止裂纹
因为振动过程中残余应力大的点首先进入屈服,所以高应力点下降的比例大,使应力均化程度高,从而降低应力集中而防止裂纹。
(2)减少或防止构件变形
构件的变形是由于残余应力特点而造成的,残余应力的分布和量值具有很大的随机性,分布不均且量值差别太大,容易产生变化,通过振动时效使应力降低和均化,必然防止或减少变形。
(3)提高焊接构件的疲劳寿命,增加使用周期。
通过大量的实验和实践证明,振动时效可提高焊件的疲劳寿命50%以上,可提高使用寿命0.5~1倍。
由于振动时效的上述作用,因此在国外得到了较普遍的应用,也得到了我国机械制造业的应用和国家主管部门的重视和认可,并于1991年制定了国家行业标准JB/T5926.91,1998年和2003年又重新进行了修订。1993年曾被国家科委批准为“科技成果重点推广计划”项目,使该项技术在全国普遍推广和应用。振动时效技术在我国已被认为是一项成熟技术,在降低和均化内应力上,振动时效可以代替热时效来处理铸件、焊接件等,具有极大的经济和社会效益。
2、减速箱壳体的振动时效处理
φ660开炼机减速箱壳体是由箱盖、中箱体和下箱体三件组成,其重量分别为1778kg、2508kg和2430kg,均由HT200材料铸造而成。结构型式复杂,厚薄不均,且有多条筋板。由于振动处理前已经初加工,故内应力分布不规律。但三件各自分别为对称结构,因此在应力测试布点只选择构件的一边;在振动处理时,其支撑方式为两边对称各放置2个橡皮垫做四点支撑。附:振动时效处理现场图
对三件箱体试验过程均为振动处理前做残余应力检测、振动时效处理、振后的残余应力检测。
一、箱体的振动时效处理
(1)试振:每种部件均选用2件,其中一件用做正式处理使用,即对该件做振前残余应力检测、振动时效处理及振后的残余应力检测。而另一件做试振用。试振的目的是初选工艺参数:激振与拾振位置、支承方式、构件共振频率及处理频率、激振器偏心等等。本次试验的每种件均通过试振给出了工艺参数,再用这个参数去处理另一件,并检验其效果。在振动时效工艺制定中,试振是一个非常重要的环节。在批量生产的构件制定工艺时,应尽量采用多件试振。本项试验中,每种件都是试振二件以上。
(2)箱体的正式处理
根据试振的如下表参数对各件进行正式处理。表一 箱体部件VSR处理参数
(3)处理曲线分析
图1~4为各件处理时的监测曲线。从曲线上不难看出经过振动时效处理,各种件均发生了固有频率下降、振幅升高等现象,说明振动时效发生了作用,即内应力降低和均化。
表二 部件振动参数的变化
二、减速箱壳体振动时效处理效果检测
振动时效处理效果一般均用振前、振后残余应力变化率来衡量其是否合格。本项试验对三种部件都做了振前、振后的残余应力检测,其应力率均达到国家标准。
测试方法采用通用的盲孔法,贴片位置见附图1~3,每个部件在振前、振后均测5点。测试结果见表三~表五。
表三 (箱盖)VSR前后残余应力测试数据 单位:MPa
表四 (下箱体)VSR前后残余应力测试数据 单位:MPa
